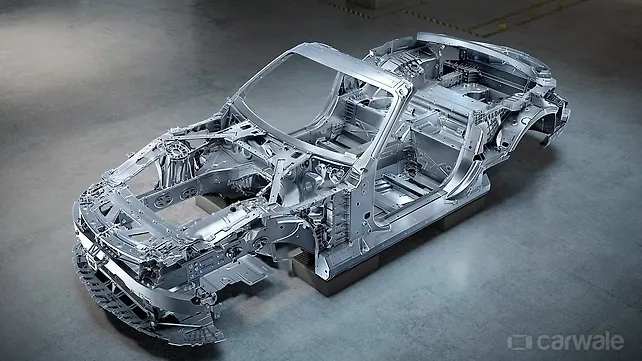
- Roadster architecture with a composite aluminium structure
- Production of the new SL will take place at the Bremen plant
Mercedes-AMG – in a run-up to the global premiere of the new-gen SL – has revealed the new aluminium chassis that would underpin the two-door roadster. The new roadster architecture consists of a combination of an aluminium space frame with a self-supporting structure.
Since the new-gen SL will be significantly different from the outgoing model – it will be for instance a 2+2 and will have more powertrain choices – the chassis has been drawn and constructed from a clean sheet of paper. The German carmaker claims that not a single component was taken over from the preceding SL model or the AMG GT Roadster. The weight of the pure bodyshell without doors, bonnet and boot lid, and any add-on assembly parts, is said to be around 270 kilograms.

Meanwhile, the entire space frame structure is more rigid – up to 18 per cent – and better weight-balanced than any roadster before, says Mercedes. The use of intelligent materials, for instance, aluminium, steel, magnesium and fibre composite, has increased transverse rigidity by 50 per cent over the AMG GT Roadster and the longitudinal rigidity is up by 40 per cent. Other targeted measures include aluminium thrust panels on the underbody and function-integrated struts at the front and rear. The instrument panel support for the MBUX is made of magnesium, along with part of the front module cover bridge made out of a fibre composite material with a mixture of glass fibres and carbon. This also applies to the windscreen frame made of high-strength and hot-formed tubular steel. And since it’s an open-top roadster, the seats that extend at lightning speed, if necessary, serve as rollover protection.

Looking at the chassis’ images, it isn’t difficult to figure out that it is geared towards attaining the lowest possible centre of gravity. Apart from that, modern joining techniques such as MIG welding, laser welding, punch riveting, blind riveting, MIG soldering, glued seams or flow-hole bolts, as well as toolmaking, are used of the highest quality. It’s also claimed that the new Mercedes-AMG bodyshell architecture meets all internal crash requirements complying with stricter legal requirements.

It took Mercedes-AMG only three months of pre-development and less than three years from the time the commission was given thanks to new-age software and digital development. Lastly, the structural verification vehicle, which is of immense importance for passive accident safety, claims to have received an internal top rating in the first real crash test.