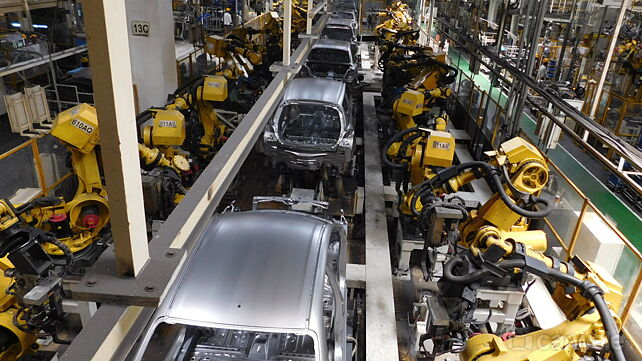
Before the launch of Maruti Suzuki’s new Dzire, the carmaker decided to show us the initiatives taken in the making of this compact sedan at the Manesar plant.
But first, let me give you a rough sketch of the Maruti Suzuki plant set up. Maruti has three facilities, one in Rohtak, where the company’s research and development wing is housed, and the other two in Gurgaon and Manesar, where the cars are produced. They currently produce 16 models and 1075 variants! While the Manesar plant churns out 3100 cars a day, the Gurgaon plant rolls out another 2700 cars. Collectively, a total of 5800 cars roll out every 16hrs, and employees are put through two shifts of eight hours each. In fact, we’re looking at a Maruti car being produced every 10sec! The Manesar plant alone has about 7000 employees and the production runs at 98 percent efficiency. Maruti exports their cars from India to at least 110 countries, and around 10 per cent of their overall production is exported. This plant facilitates a planned shutdown for one week to carry out maintenance work, and this is done twice a year (every six months).
From the outside, the Manesar factory is so vast that it easily takes ten minutes of driving just to go around the factory gates. We were told that on any given day, close to 2500 vendors get their components into the factory and around 3400 trucks enter the premises. And if you thought that wasn’t an eye-ball grabbing scene, read further. Model and variant requirements are frozen five days in advance as vendors also provide their components as per the vehicle-build-sequence. This is a detailed list of what is being built for the next few days. The production line we visited makes the new Dzire, Swift and Ciaz on the same line in alternating sequences and colours, and components are fed onto this line as per this vehicle-build-sequence. Let’s look at the basic processes involved in making a car. It starts at the press shop and moves on to the weld shop before going through the paint shop. From here the car is then transferred to the assembly line before finally getting the vehicle inspection carried out. We have already covered the basic processes here.
To demonstrate their focus on the work environment, Maruti Suzuki looks at four parameters; safety, quality, ergonomics and flexibility. Let’s look at the safety aspect first. The company puts safety on high priority and it is done on every level which includes the plant, shop and station level. Since every job is different, it calls for varying levels of safety – for example, the safety parameters for the weld shop will be different than that of the press shop. Nevertheless, there’s 100 percent adherence to personal protective equipment (PPE) like cut-resistant Kevlar gloves for handling sharp objects, helmets, safety goggles and denim-based arm covers. Even advanced safety initiatives like area sensors are used to detect human presence in automated stations.
When it comes to quality, Maruti Suzuki aims for zero defects and they prefer to focus on building products better, instead of focussing more on inspecting processes. Nevertheless, the press shop uses workers who visually inspects the panels and doors for any mistakes. Similarly, the weld shop uses 100 percent robotic welding to ensure quality real-time spot welding, and the inspection is automatically carried out by the system. However, the assembly shop uses a fool-proof process called ‘pika pika’ to prevent mistakes from happening. In this process, if the technician picks up the wrong component, the system alarm goes off and the production line stops. Furthermore, the plant also facilitates the use of cordless limit wrenches (CLW) for a given torque, and parts scanning to make sure the correct components are fitted on to the right car (for example, scanning of headlamps and airbags). Tablets are also used at some stations for the inspection procedure.
Maruti Suzuki uses rapid entire body assessment (REBA) for appropriate ergonomics. It is a scientific method to assess the technician’s body parameters so that the machine adapts as per the work conditions and operator’s height at various stations. This is mainly done to reduce the fatigue and can be seen in the height adjustable conveyors that adjust along the production line. Then there’s the synchro trolleys, turn tables and power-assisted lifters that allows workers to efficiently carry out their jobs without walking a lot, and also help them lift heavy objects like batteries, axles and doors like Arnold Schwarzenegger from ‘Terminator’. The production plant is also flexible so that the output can be tweaked to cater to our market’s seasonal demand. Other points that highlight the flexibility of the output is the dual stamping that is carried out in press shop to produce similar and dissimilar panels simultaneously in one stroke. Again, the robots are extremely flexible and are able to automatically change the hands for jobs pertaining to different cars on the same production line, with the ability to paint 48 colours in any sequence!
Now if you thought robotic automation cost human’s their jobs, you would be surprised to know that Maruti Suzuki does not believe that robots will take over eventually. They added that robots are used only when the job is difficult, dangerous and dirty. As a matter of fact, in the last decade or so, the requirement for more features in a car has exponentially risen, and all these features are fitted by human hands at the plant. So, on the contrary, Maruti expects that the increase in feature requirements is going to fuel the requirement for even more human hands at the plant. Food for thought?
What you didn’t know about Maruti’s new Dzire
How your shiny new Dzire is made
New 2017 Maruti Suzuki Dzire launched at Rs 5.45 lakh
Pictures: Venkat Desirazu & Santosh Nair