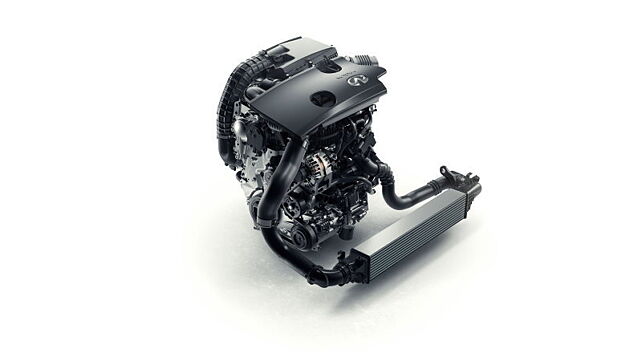
Technology evolves slowly unless there comes a breakthrough that takes it a step above. The new VC-T engine developed by Infiniti, Nissan’s luxury arm, seems like the step engine technology is about to climb. We delve deeper into their patent drawings to find out how it works while giving out a geek alert to our readers.
The barrage of small turbocharged petrol engines started with Ford’s EcoBoost and now we have an indigenous Revotron built by Tata Motors. The reduced displacement promised better emissions to match the stringent norms and also better fuel economy. While the engines stood their ground on emissions, they did not deliver much on the fuel economy front and that is due to its design. As we all know, turbocharged engines run on a lower compression ratio to factor in for the higher pressure in the combustion chamber due to forced induction when the turbo spools up. This may result in premature detonation of the fuel charge resulting in loss of efficiency and power and also may stress the engine internals to failure.
When the turbocharger is yet to spool up (which is generally near the 2000rpm range), the engine is running low compression. In city traffic, cars do not really rev high and are caught in turbo lag more often than not. The engine, hence, guzzles more fuel every time you step on the throttle to compensate for the lower compression. The Infiniti VC-T claims to run variable compression – high compression when the engine is under load through turbo lag and low compression when the turbo spools up. While that seems easy on paper, building a variable compression engine to deal with the thermal and mechanical stresses is a different ball game altogether.
Infiniti has devised an ingenious method evident from its patent drawings. The engine runs on variable crank radius which helps shift the top dead centre of the piston towards or away from the cylinder head, thus, varying the compression ratio. To achieve the required shift, instead of assembling the connecting rod on the crank pin, Infiniti engineers have pivoted a bell crank linkage on the crank pin to one end of which the connecting rod is fixed. The crank pin acts as fulcrum and the position of the link is monitored by a control shaft attached to the other end. The control shaft is controlled by the actuator arm which is electronically operated by the ECU.
When the engine starts, it runs high compression (14:1) with the actuator stretched out – running like a normal naturally aspirated engine. As the turbo spools up and starts forcing air into the combustion chamber, the ECU pulls the actuator arm in lowering the compression ratio in the combustion chamber to as low as 8:1. This helps in achieving minimal fuel consumption in both cases and also ensures complete combustion and low emissions in all scenarios.
The 2.0-litre VC-T develops 268bhp of power and 390Nm of torque. While it is not the highest in terms of power output for similar-spec engines, the torque output is at par with the leaders. It also claims to offer a better torque curve and 27 per cent better fuel economy overall. What it also means is the engine construction will become more complicated, more dependent on electronics and sensors and with more mechanical linkages may incur higher friction losses. The real test for this new concept is real world performance. We will have our fingers crossed to see if it delivers and becomes the next step in engine technology.