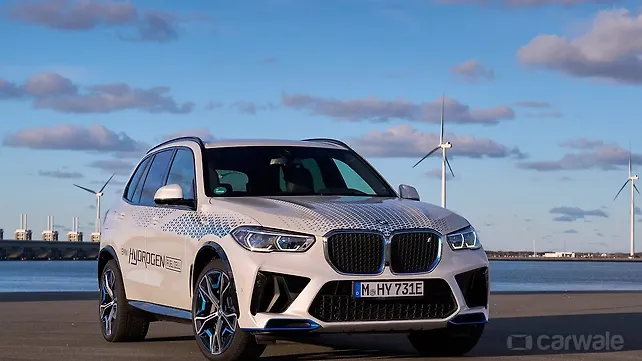
- Test vehicles in real-world use
- Paving the way for potential production
After four years of development work, the BMW iX5 hydrogen car and its development project are entering its critical next phase as the first vehicles enter a pilot fleet of under 100 vehicles. The fleet is being deployed internationally for demonstration and trial purposes. This active driving experience will be the first chance for people not involved in the development process to gain an impression of what the iX5 hydrogen has to offer.

BMW iX5 hydrogen details
The BMW iX5 hydrogen developed on the basis of the current X5 was first unveiled as a concept at the IAA show in 2019. Initial prototypes were then made available at the IAA Mobility 2021 for visitors to experience in action as shuttle vehicles. The fuel cell systems for the pilot fleet have been developed at BMW’s in-house competence centre for hydrogen in Munich. The tech generates a continuous output of around 170bhp.

The hydrogen needed to supply the fuel cell is stored in two 700-bar tanks made of carbon-fibre reinforced plastic (CFRP). Together these hold almost six kg of hydrogen, enough to give the iX5 hydrogen a range of 504km in the WLTP cycle. Filling up the hydrogen tanks only takes three to four minutes.
How the iX5’s fuel cell system works
A chemical reaction takes place in the fuel cell between gaseous hydrogen from the tanks and oxygen from the air. Maintaining a steady supply of both elements to the fuel cell’s membrane is of crucial importance for the drive system’s efficiency. In addition to the tech equivalents of features found on combustion engines, such as charge air coolers, air filters, control units and sensors, BMW has also developed special hydrogen components for its new fuel cell system. These include the high-speed compressor with turbine and high-voltage coolant pump, for instance.

BMW sources the individual fuel cells from Toyota. The two companies have been collaborating on fuel cell drive systems since 2013. Now, the fuel cell systems are manufactured in two main steps, based on the individual fuel cells. The cells are first assembled into a fuel cell stack. The next step involves fitting all the other components to produce a complete fuel cell system.
Final assembly of the fuel cell stacks includes a voltage test along with extensive testing of the chemical reaction within the cells. Finally, all the different components are fitted together in the assembly area to produce the complete system. During this system assembly stage, further components are fitted, such as the compressor, the anode and cathode of the fuel-cell system, the high-voltage coolant pump and the wiring harness.